Keraplast Manufacturing, Christchurch
Keraplast Manufacturing in Christchurch required a single head filling machine to fill medical gel into two different aluminium tubes, on an existing rotary table that was used for crimping tubes.
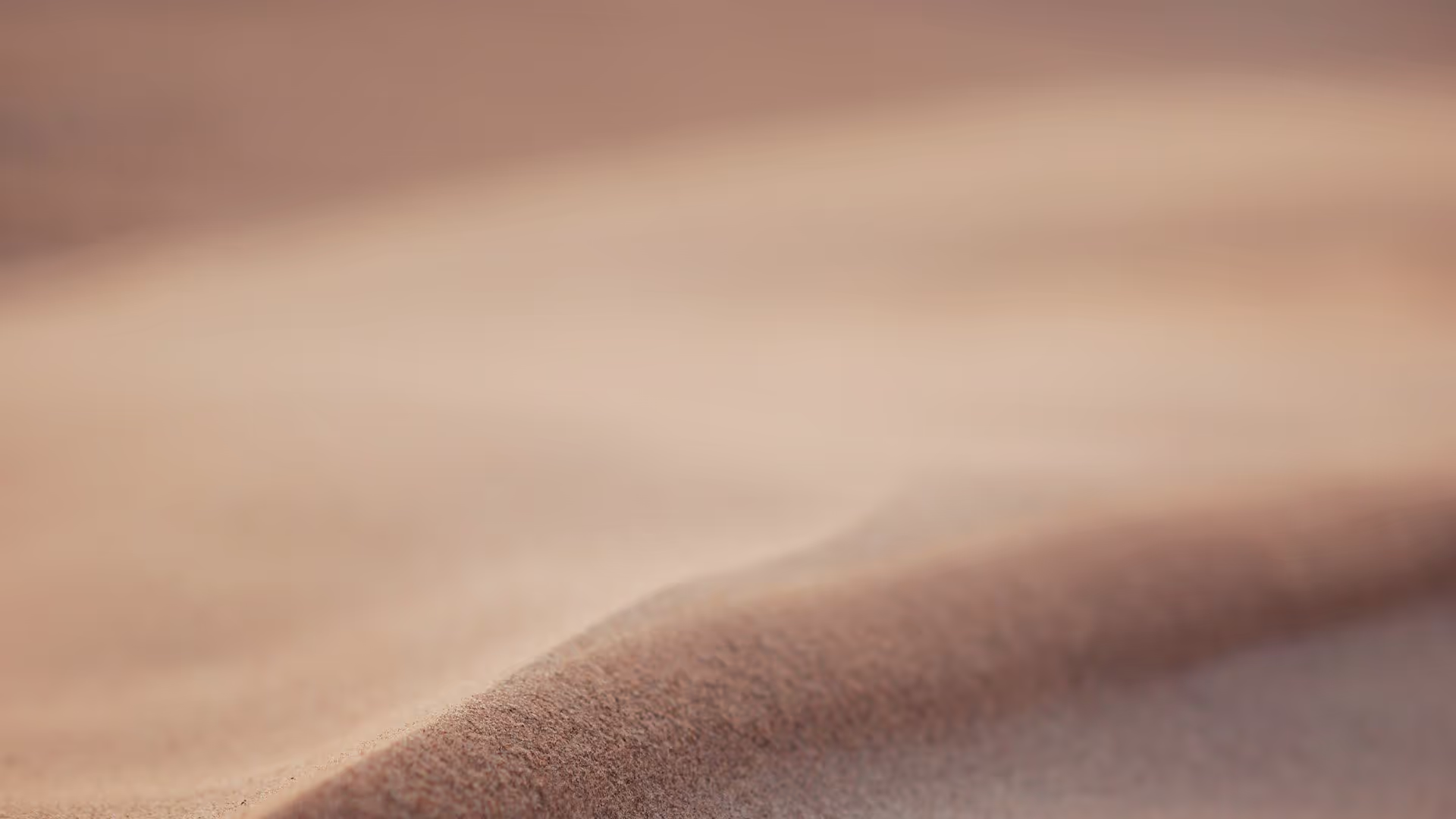
Keraplast Manufacturing successfully integrated a new filling system with their existing rotary table, achieving precise, air-free filling of medical gel into aluminium tubes. The final solution met the customer's expectations, seamlessly blending new technology with existing equipment.
The Challenge
Keraplast Manufacturing in Christchurch faced several unique challenges:
The Solution
Hunter Filling Systems provided a customised, precision-engineered solution:
Specialised Filling Machine:
Custom Integration:
Air-Free Filling Technology:
Smart Detection System:
Versatile Design:
Through persistent refinement and attention to detail, Hunter Filling Systems successfully integrated the new filling technology with Keraplast's existing equipment. This meticulous approach ensured that the final solution precisely met the customer's unique requirements for their medical gel product.