Pack Logix, USA
Hunter Filling provided Pack Logix with a four head Hunter model 1545 with top fill and bottom up fill nozzles to accommodate the range of container sizes and product viscosity for this contract packer of automotive products.
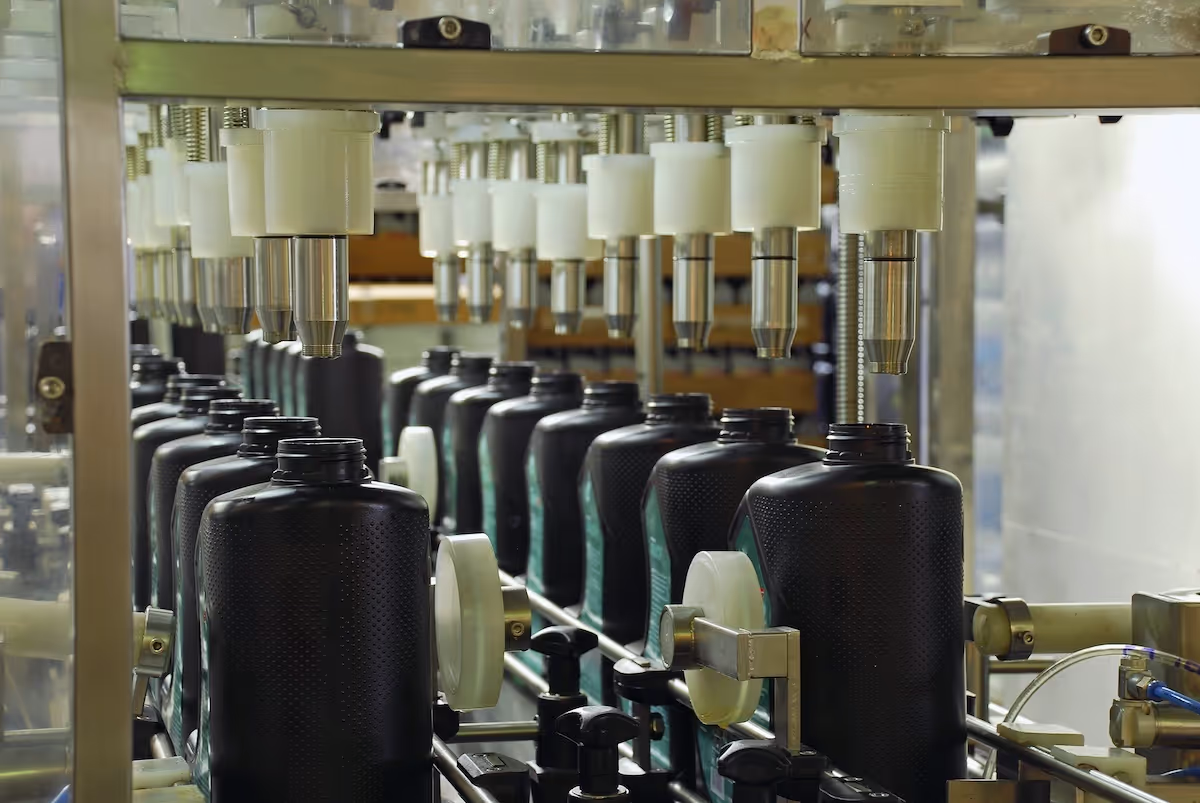
Pack Logix achieved quick changeover times and minimal filler downtime, thanks to Hunter Filling's easy-to-clean design. The versatile solution accommodates a wide range of products and container sizes, enabling Pack Logix to efficiently meet the diverse needs of their automotive industry clients.
The Challenge
Pack Logix, a US-based contract packer of automotive products, faced several complex challenges:
The Solution
Hunter Filling Systems provided a customised, multi-faceted solution:
Filling Machine: A Hunter model 1545 with four filling heads, featuring:
Versatile Design: The machine's adaptable configuration allows for:
Optimised for Efficiency:
Through extensive product testing and trials, Hunter Filling Systems tailored this solution to meet Pack Logix's specific needs, resulting in a highly efficient and flexible filling system for their diverse automotive product line.
Lanocorp Pacific Ltd
Productivity and Precision
The Result
Lanocorp Pacific Ltd significantly increased their production and achieved more accurate filling for their face cream and lotion line. The transition from a single-head semi-automatic system to a twin-head fully automatic filling solution streamlined their operations and enhanced overall productivity.
The Challenge
Lanocorp Pacific Ltd in Christchurch faced several key challenges:
The Solution
Hunter Filling Systems provided a comprehensive, automated solution:
Filling Machine: A Hunter model 325B two-head filler, featuring:
Versatile Design: The system was tailored to meet Lanocorp's diverse needs:
Improved Accuracy and Speed:
By transitioning from a single-head semi-automatic system to this twin-head fully automatic solution, Hunter Filling Systems helped Lanocorp Pacific Ltd achieve a significant boost in productivity while maintaining the high-quality standards required for their face cream and lotion products.