Lanocorp Pacific Ltd, Christchurch
The client were wanting to increase productivity from a single head semi automatic to twin head fully automatic filling on a conveyor for an automatic face cream and lotion filling line for small containers.
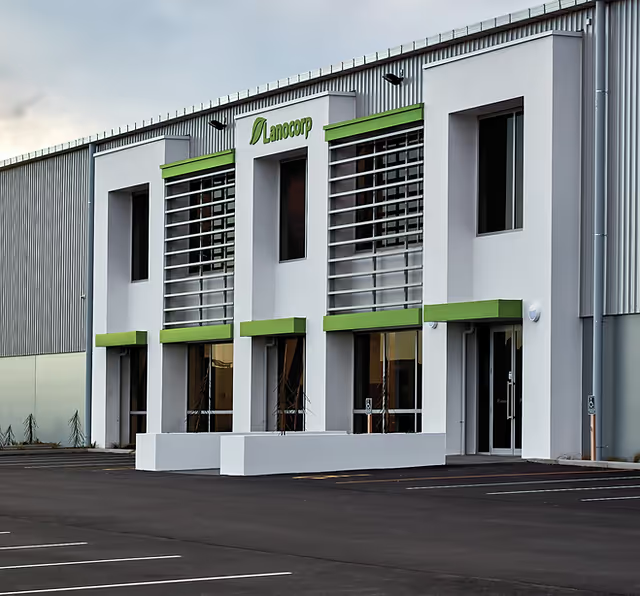
Lanocorp Pacific Ltd significantly increased their production and achieved more accurate filling for their face cream and lotion line. The transition from a single-head semi-automatic system to a twin-head fully automatic filling solution streamlined their operations and enhanced overall productivity.
The Challenge
Lanocorp Pacific Ltd in Christchurch faced several key challenges:
The Solution
Hunter Filling Systems provided a comprehensive, automated solution:
Filling Machine: A Hunter model 325B two-head filler, featuring:
Versatile Design: The system was tailored to meet Lanocorp's diverse needs:
Improved Accuracy and Speed:
By transitioning from a single-head semi-automatic system to this twin-head fully automatic solution, Hunter Filling Systems helped Lanocorp Pacific Ltd achieve a significant boost in productivity while maintaining the high-quality standards required for their face cream and lotion products.
Wet & Forget
Exceeding expectations and accelerating the time to market
The Result
Wet & Forget achieved a significant reduction in their product delivery time to market. The customised filling solution not only met but exceeded their expectations, enabling efficient handling of diverse products and container sizes while minimising foaming and changeover times.
The Challenge
Wet & Forget in Auckland faced several complex challenges:
The Solution
Hunter Filling Systems provided a tailored, high-performance solution:
Advanced Filling Machine: A four-head subsurface filling machine, featuring:
Customised Design:
Efficiency Optimised:
Collaborative Approach:
By providing a filling solution that addressed all of Wet & Forget's unique challenges, Hunter Filling Systems helped the company streamline their production process, resulting in faster delivery times and a system that surpassed their initial expectations.